
Using a cheaper building material that takes less time to put up could help.Ĭarolyn Hyman, a spokeswoman for Aloha United Way, which is working to find solutions to Hawaii’s high cost of living, said generating less expensive housing is what locals need. The state has the nation’s fourth lowest homeownership rate at 58%, behind only the District of Columbia, New York and California, according to fourth quarter 2021 census data. Housing advocates hope pre-fab construction can translate into more people owning homes in Hawaii. SIP Systems Hawaii co-founder Brian Enomoto talks about the sustainability of the wood products at a residential project located on 10th Avenue in Kaimuki. “It’s really hard to compare the total costs, but our biggest savings is for labor on the framing and saving monthly on energy efficiency,” said SIP Systems Hawaii co-founder Brian Enomoto. So, based on the mid-point of $540, building an 1,800-square-foot single-family home in Honolulu would cost nearly $1 million - that’s if the developer did not mark up the house for resale.Ĭompare that to a house twice that size, for example the 3,500-square-foot home on 10th Avenue that SIP Systems Hawaii has in the works: its projected construction costs are on the lower end at $300 per square foot, so about $1.1 million for a home twice the size. Home construction costs in Hawaii average between $295 and $785 per square foot, according to the Rider Levett Bucknall construction cost indicator. A house can be built with the prefabricated panels in less than a week, company officials say. SIP Systems Hawaii is using an innovative building material - structural insulated panels - that cuts labor costs, significantly reducing the price of the home.
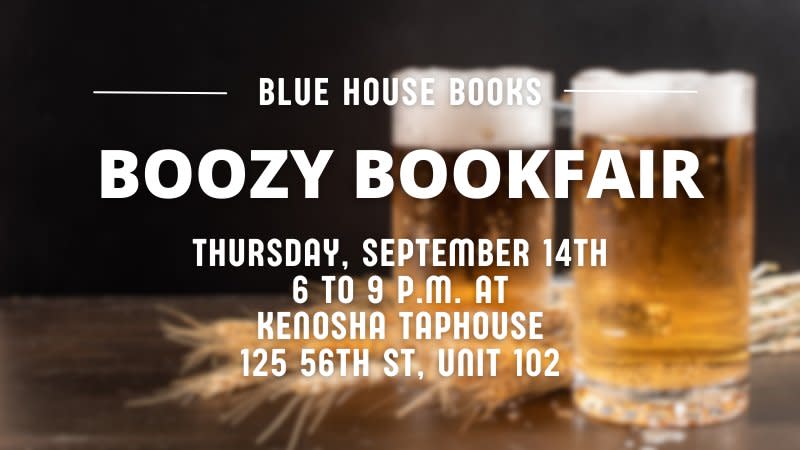
A Kaimuki company is working to address one of the biggest contributors to the high cost of living in Hawaii: housing.
